KRAL GmbH is one of the leading international specialists for screw pumps and flow measurement technology. The Vorarlberg-based family business, headquartered in Lustenau, supplies its customers worldwide, mainly in the marine, power generation, oil & gas, mechanical engineering and chemical industries. In order to strengthen its innovation and competitiveness on the international market, our customer decided to invest in the automation and digitalization of its company.
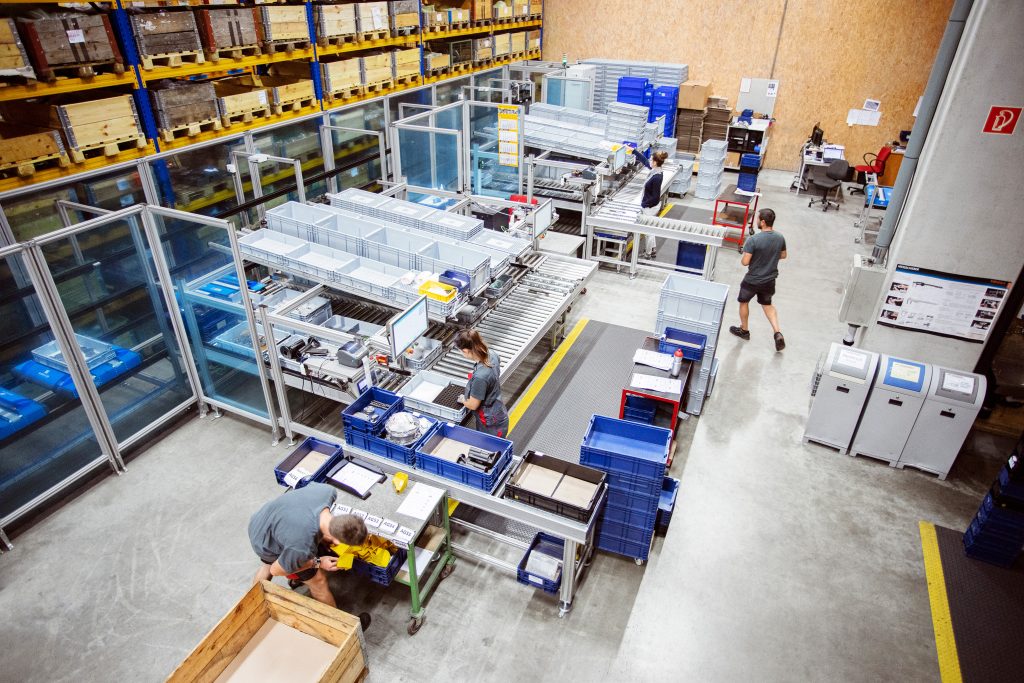
Automation and digitalization of all processes and workflows
The project started in February 2018 and was divided into several sub-projects over a period of 18 months. KRAL deliberately relied on its own employees and suppliers from the region to implement the project.
In order for KRAL GmbH to become one of the best automated and digitalized SMEs in the mechanical engineering sector in Vorarlberg, the following project scope was implemented within the specified timeframe:
- Update of the existing ERP system
- New construction of the ASRS
- Servus driverless transportation system
- MIA Warehouse Management System (WMS)
- Production machines
- Test bench
- Assembly workstations
- Production planning system
We actively supported our customer in defining the new logistics processes and were responsible for drawing up the specifications. In the process workshops not only were customer-specific processes visually represented with interactive GUI prototypes, but feedback was also integrated at an early stage. Thanks to this method, the customer’s comments were incorporated into product development at an early stage. This resulted in a quick understanding among all participants and short decision-making paths, which contributed significantly to the success of the project.
New warehouse management system for all logistics processes
The overall project was seamlessly integrated into the day-to-day business and into the existing structure and infrastructure. As a result, KRAL did not have to postpone any customer orders.
Mobile devices were used in the manual storage sections. Thanks to our mobile solution, MIA Mobile, all work processes were accelerated and optimized. At the same time, the processes at the stations of the Servus system were mapped using MIA I-Point Touch. Thanks to the simple and intuitive interface of our WMS, employees were able to shorten their training period and quickly overcome their initial fears.
The existing ERP system had to undergo a complete upgrade for the transport system and WMS connection to work. Once the necessary adjustments had been made, the interface was set up quickly and stably without any major delays.
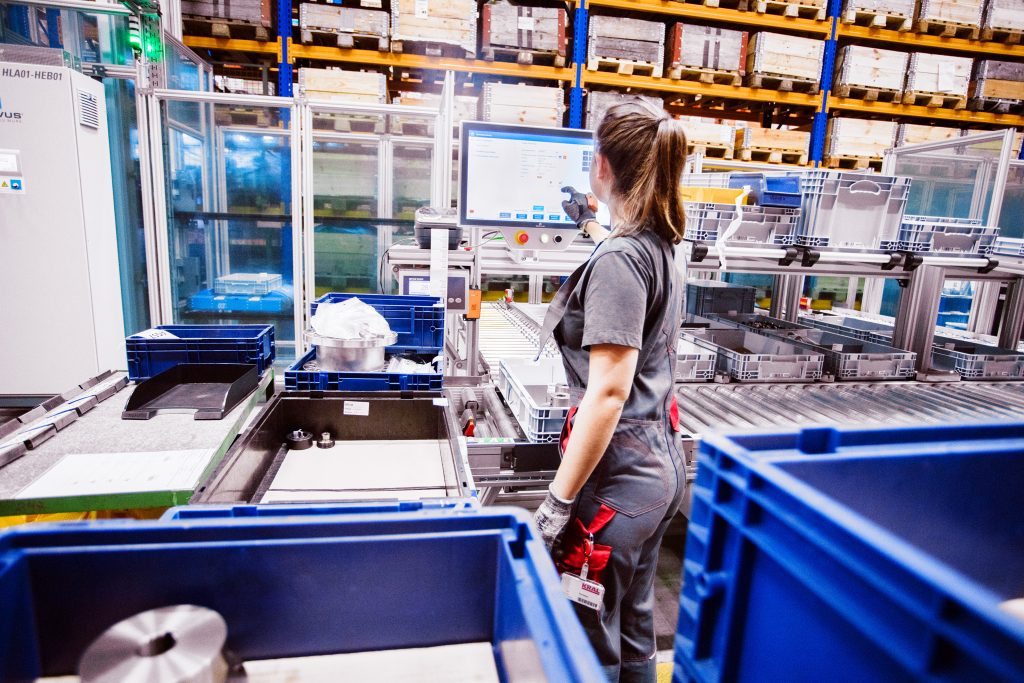
A project for the future
This project has laid the foundation for further upgrades in digitalization and automation at KRAL GmbH. The project is a key building block for future success. Throughput times have been reduced by 50% since the changeover.
KRAL GmbH won the 2020 Logistics Award for this successful regional project. The decisive factor for the jury was the shortening of the lead time in production in order to improve the response time on the market.
Factbox
- Number of employees working with MIA/Servus: 20
- Number of picking positions per day: approx. 1010
- System performance (storage and retrieval /h): approx. 2539 calculated in 8h 318 trips/h
- Number of parking spaces: 9500
- Number of arcs: 22