Together with Servus Intralogistics, MIA Systems was involved in the digitalization and automation of our customer Hirschmann Automotive at the Vsetín site in the Czech Republic. One year after the go-live, a KVP meeting with the entire project team took place on site last week.
Hirschmann Automotive relied on the smart production concept for the expansion of its competence center for injection moulding technology in Vsetín (Czech Republic). The Warehouse Management System (WMS) from MIA was connected to the ERP system (SAP) and manages all logistics processes relating to production and shipping logistics. The WMS is also responsible for storage location management in the small parts warehouse, storage, delivery to assembly and consolidation in shipping.
The focus is on the approx. 60 connected injection molding systems, which are operated fully automatically. Thanks to optimally adapted automation, both the delivery of empty containers and the collection of filled containers and cartons are fully automated.
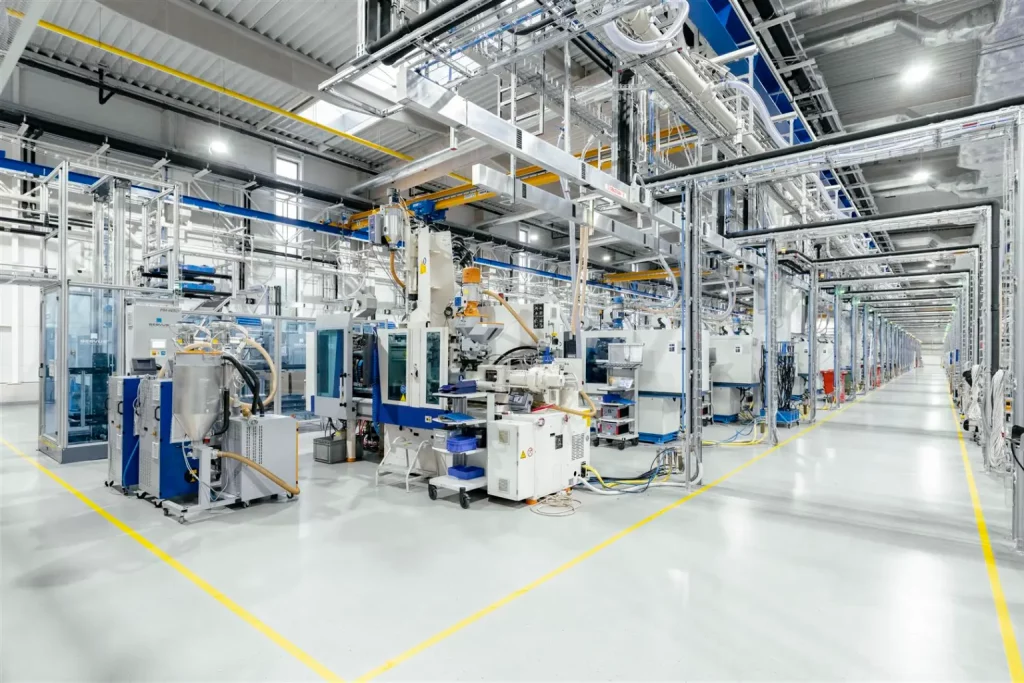
One year after the go-live, a KVP meeting was held on site with the entire project team of all those involved to gather feedback from users. The aim was to check which areas could still be fine-tuned. We were able to find the one or other adjustment screw during these days and make an adjustment directly on site.
This example shows very clearly that our projects do not end with the go-live. The continuous improvement process ensures that existing processes are constantly monitored and reviewed. This gives the customer a logistics system with a guaranteed future, which grows with internal requirements and those of the market and is also constantly optimized.
Source Pictures: Hirschmann Automotive