Lechler GmbH, based in Metzingen, is actively investing in its site in Germany. A new logistics center with a fully automated small parts warehouse is being built on an area of 5,300 square meters. In addition, the existing production hall is being expanded to increase production capacity.
Lechler employs around 780 people worldwide, 360 of whom work at the Metzingen site, and is one of the leading manufacturers of nozzle technology. With over 140 years of experience and more than 45,000 nozzle variants, the company serves numerous industries, processes and applications. As a reliable supplier, the internationally present Lechler Group focuses on high manufacturing flexibility and outstanding quality.
Due to the growth of the international Lechler Group and its function as a central logistics hub with direct shipping to customers, an innovative solution is needed to meet future requirements. The construction project for the new logistics center at the headquarters in Metzingen started at the beginning of 2020. With an investment of around 19 million euros, the company will serve its customers even more efficiently in future and also take its logistics processes to the next level.
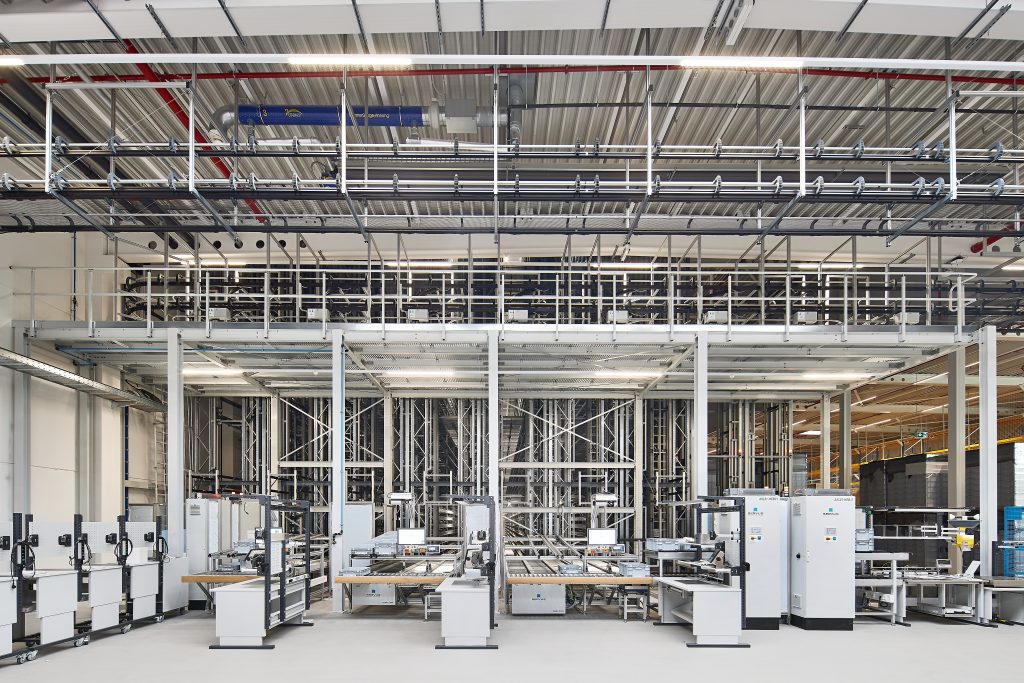
Automated small parts warehouse with 45,000 bin storage locations
The outdated small parts warehouse with stacker crane was replaced by a space-saving, automated small parts warehouse. Here, Lechler relies on intelligent, autonomous transport robots from Servus Intralogistics in Dornbirn. The new small parts warehouse offers around 45,000 storage locations, while the high-bay warehouse has a further 900 pallet spaces. In addition, the quality assurance and packaging areas were connected directly to the retrieval lane in order to optimize processes
As the existing MFR solution could not be further developed, the company opted for the WMS system with integrated pick-by-light solution from MIA Systems. The MIA WMS controls the automated small parts warehouse and maps the logistics processes at the individual stations using MIA I-Point Touch. By illuminating the bin compartments to be picked, the picking precision increases noticeably, minimizing picking errors. The flexible compartment subdivision of the bins and the option of compressing storage units with the WMS create significantly more space in the warehouse. In addition, the intuitive UI design with specialist visualization simplifies operation and ensures fast onboarding of new employees.
“Throughout the entire project, there were always open discussions at eye level, as well as the willingness of all project participants to rethink and redesign processes and solutions. There was always a good spirit and great collaboration. Especially in the Hypercare phase, there was very close and rapid coordination between the entire team in all areas.”
Maxim Weinmann, Leiter Logistik bei Lechler GmbH
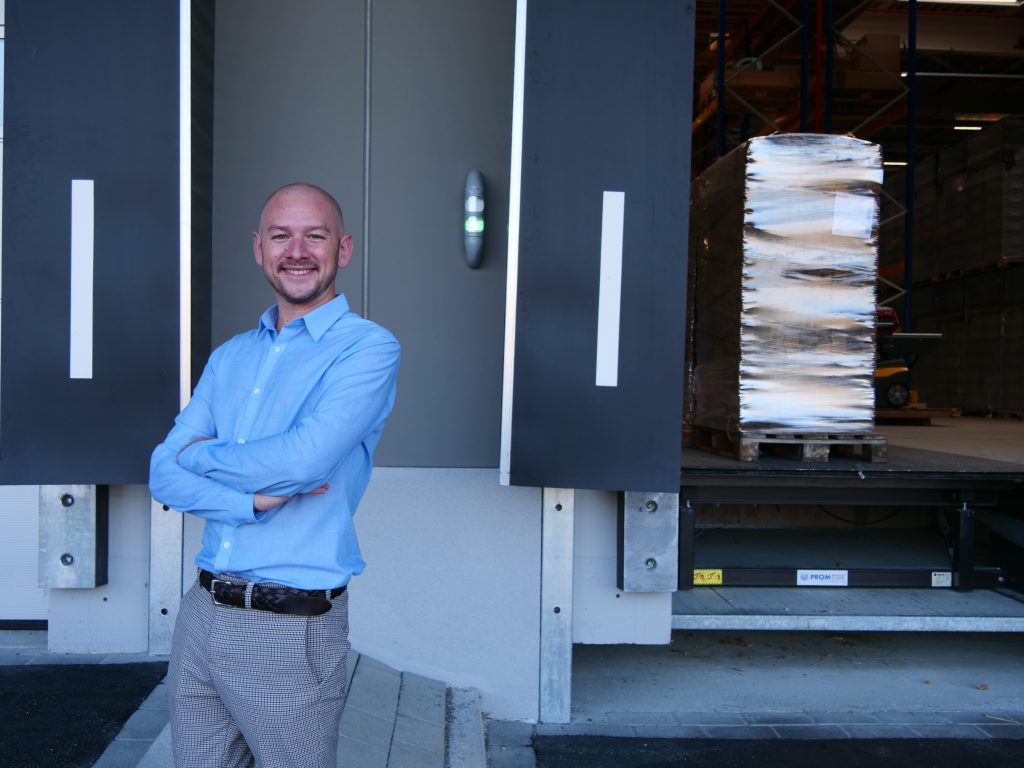
Rethinking and redesigning processes and solutions
“With our new shuttle AS/RS, we have taken our warehouse processes to the next level,” said Maxim Weinmann, Head of Logistics at Lechler. “In addition to optimizing the picking processes, our main focus is on the reliability of the warehouse. The project team achieved great results here, developed a solution that was ready for use from go-live and gives us the opportunity to integrate additional processes in the future.”
Factbox
- Number of employees on the Servus system: 16
- Number of storages per hour: ~ 150
- Number of picks per day: ~ 1000
- Number of transport robots: 15
- Automatic small parts warehouse:
- 7 aisles with 32 levels
- 45,000 storage locations
- 2 different bin heights